Prefabricated Rubber Track Construction Process
- Share
- publisher
- Donna
- Issue Time
- Jun 28,2024
Summary
A prefabricated rubber track is a type of athletic surface made from pre-manufactured rubber sheets or modules. These sheets are designed to provide consistent performance, durability, and safety for various sports activities. The prefabricated nature of the track allows for quicker and more efficient installation compared to traditional poured-in-place surfaces, ensuring a high-quality finish with uniform thickness and texture.
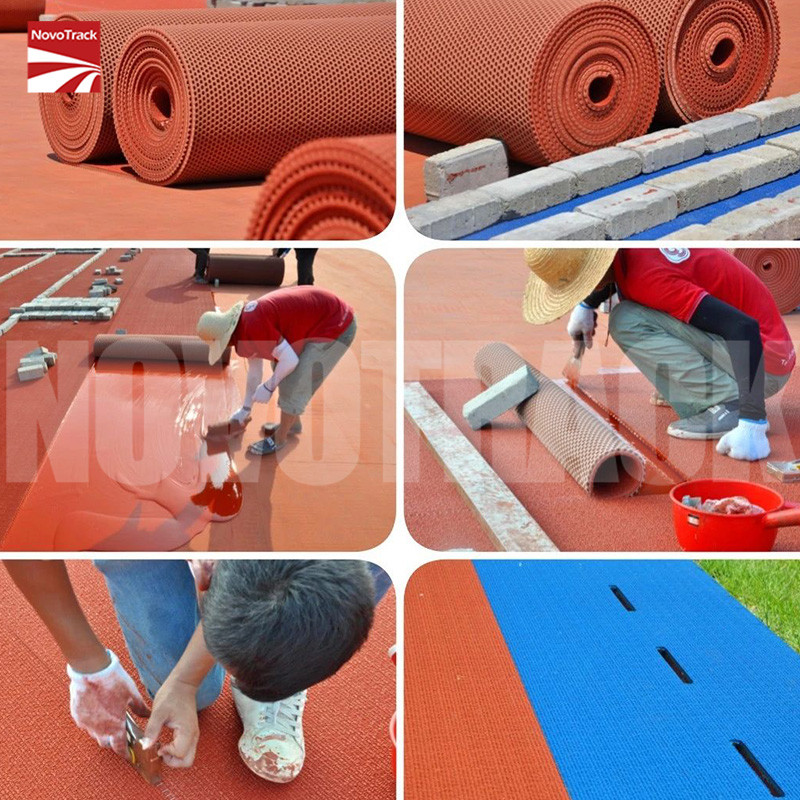
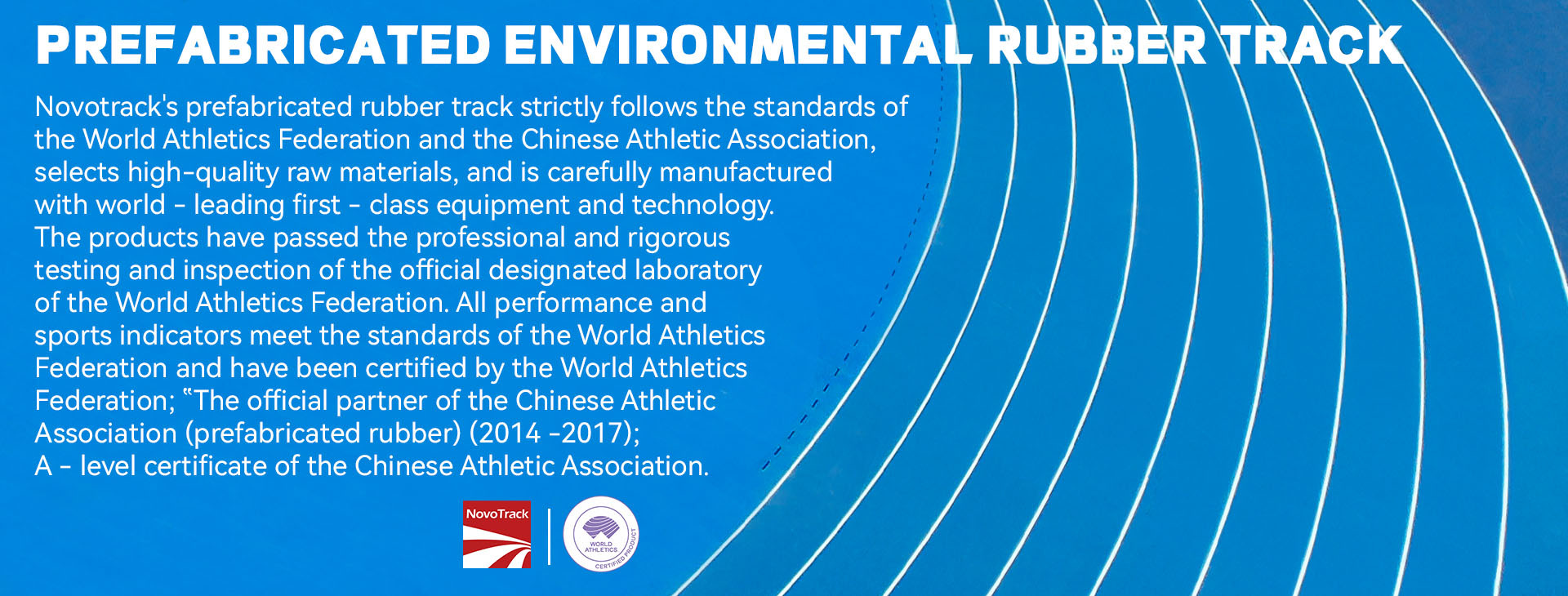
A prefabricated rubber track is a type of athletic surface made from pre-manufactured rubber sheets or modules. These sheets are designed to provide consistent performance, durability, and safety for various sports activities. The prefabricated nature of the track allows for quicker and more efficient installation compared to traditional poured-in-place surfaces, ensuring a high-quality finish with uniform thickness and texture.
The track typically consists of two main layers:
1. Surface Layer: The top layer is made from high-quality, wear-resistant rubber that provides a smooth and resilient surface. This layer ensures excellent traction, reduces the risk of injury, and enhances athletic performance.
2. Base Layer: The bottom layer is composed of a thicker, shock-absorbing rubber material that provides cushioning and support. This layer helps to absorb impact, reducing stress on athletes' joints and muscles, and contributes to the overall durability and longevity of the track.
This type of track is commonly used in schools, sports facilities, and professional arenas.
Installation Process
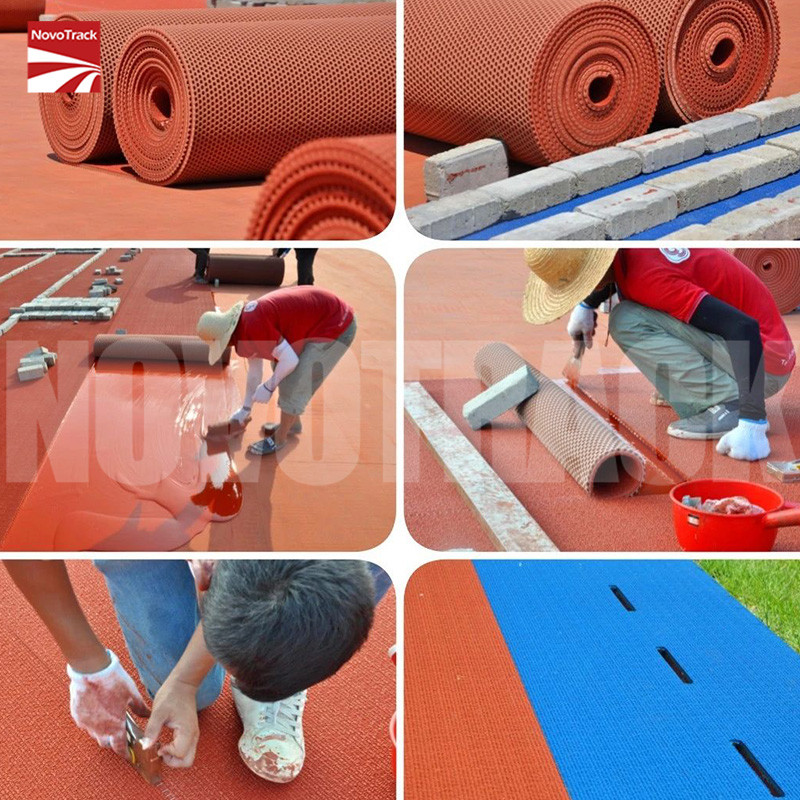
1. Clean and clear the site
2. Re-inspect the base (test for water accumulation and level the surface)
3. Pre-installation positioning
4. Install the prefabricated rubber sheets
5. Local adjustments
6. Clean the site
7. Position marking
8. Line marking
Construction Method for the Rubber Surface Layer
1) Detection and Treatment Methods for the Base Layer:
A. The detection methods for the base layer can refer to the national standard. Our product is certified by the International Association of Athletics Federations (IAAF) also called World Athletics.
B. The prefabricated rubber track has strict requirements for the flatness, strength, and density of the base layer. When the base layer meets the technical requirements for the rubber sheet surface layer construction, the next construction procedure can proceed. If the base layer does not meet the technical requirements, relevant repairs should be made based on the specific situation to achieve the required standards.
C. Base treatment: Test for water accumulation and mark the areas → Grind the raised areas to meet standards, and level the sunken and water-accumulated areas using leveling adhesive → Test for water accumulation again, and if necessary, continue leveling until there is no significant water accumulation.
2) Construction Method for the Prefabricated Rubber Track Surface Layer:
The general order of construction: main competition area → semicircular area → auxiliary area, etc.
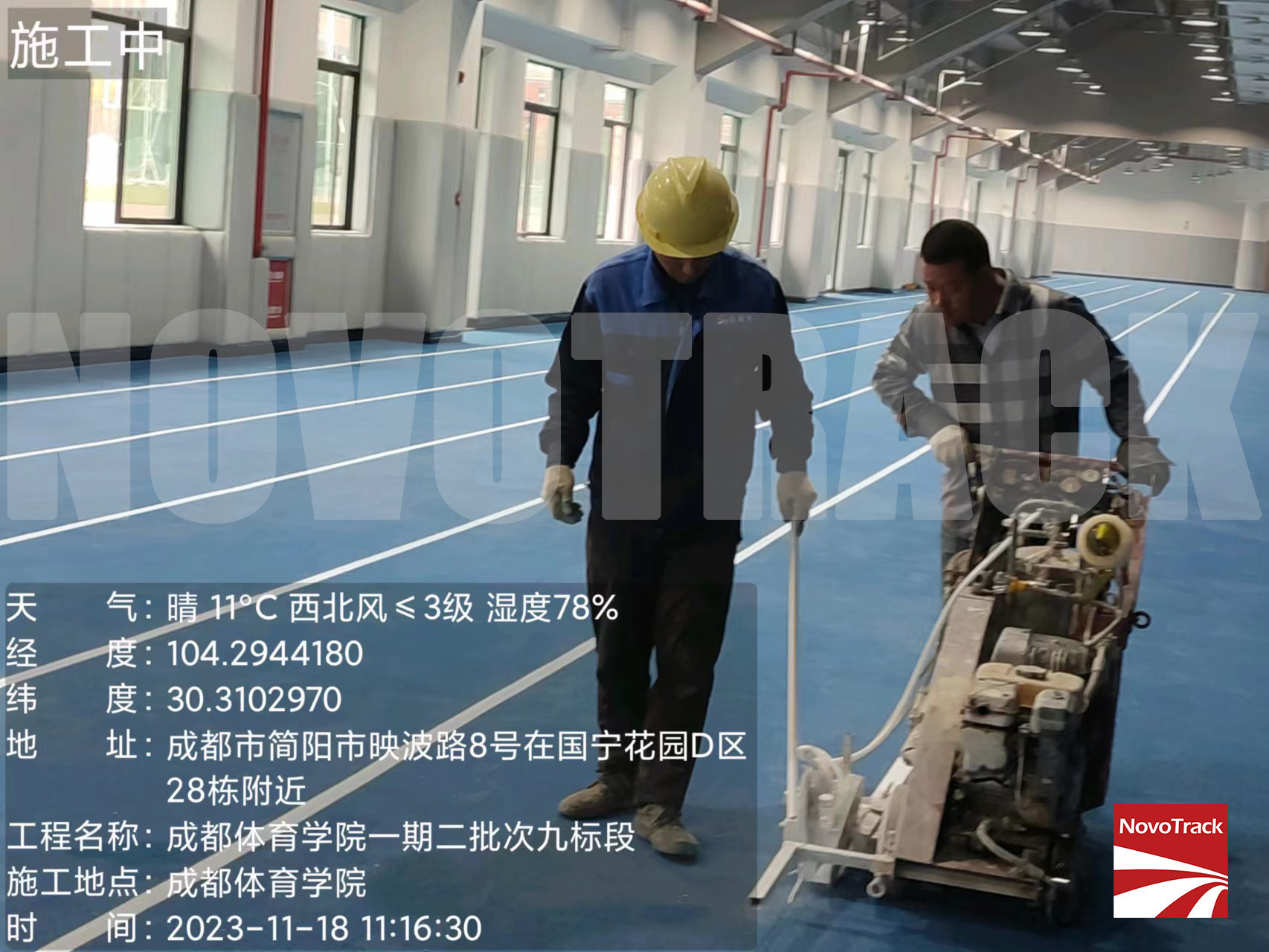
Line Marking
A. Line marking material: Use elastic polyurethane professional line marking paint. (Different white line paints have different mixing ratios, typically as follows: curing agent: thinner = 1:0.4:0.2-0.5. Mix the white paint and curing agent thoroughly before adding the thinner.)
B. Material characteristics: Wear-resistant, hydrolysis-resistant, strong adhesion, and strong color retention.
C. Layout and measurement: Use a calibrated total station and 100m steel tape measure to set point lines. Each point line should meet the track/field requirements, with an internal control index relative error of ±0 to ±1/10000.
D. Measurement and marking of the lines: After laying out the lines, the contractor provides the marking data (attached in a table), which must be confirmed by the client and the supervisor before marking the lines on the track/field. The lines should be clear and accurate.
Line Marking Precautions:
A. Measure and determine the position of various marking lines according to the marking data. Repeatedly measure and check to ensure the required accuracy. Only after confirming the accuracy should the markings be made on the rubber surface using large head pins and chalk lines.
B. The layout must be reviewed by sports technicians. The angles should be checked using the radiating line length, and straight lines should be re-checked using a calibrated steel tape (including length and temperature corrections). Confirm compliance with standards before proceeding with line spraying.
C. During line spraying, repeatedly check the width of the spraying wooden box or the spraying nozzle of the marking machine to ensure it meets the IAAF regulations. Adjust if necessary.
D. The operator should control the distance and angle of the spray gun from the rubber surface to ensure the aesthetics and uniform color of the lines.
Clean the Site and Organize Acceptance
1. Clean the site thoroughly and inspect for any issues, addressing them as needed.
2. Organize acceptance and hand over for use.